Destylator przemysłowy to urządzenie, które odgrywa kluczową rolę w procesach separacji cieczy na podstawie różnic w temperaturze wrzenia. W przemyśle chemicznym, petrochemicznym oraz spożywczym destylatory są wykorzystywane do oczyszczania i wydobywania różnych substancji chemicznych. Proces destylacji polega na podgrzewaniu cieczy do momentu, gdy zaczyna parować, a następnie schładzaniu pary, aby skondensować ją z powrotem w cieczy. W przemyśle najczęściej stosuje się destylację prostą oraz frakcyjną. Destylacja prosta jest używana do oddzielania substancji o znacznej różnicy temperatur wrzenia, podczas gdy destylacja frakcyjna pozwala na bardziej skomplikowane separacje, co jest szczególnie ważne w przypadku mieszanin wieloskładnikowych. Przykłady zastosowań destylatorów przemysłowych obejmują produkcję alkoholu, oczyszczanie wody oraz wydobywanie olejków eterycznych z roślin.
Jakie są rodzaje destylatorów przemysłowych i ich funkcje
W przemyśle można wyróżnić kilka rodzajów destylatorów, które różnią się konstrukcją oraz przeznaczeniem. Najpopularniejsze z nich to destylatory prostokątne, kolumnowe oraz wirówkowe. Destylatory prostokątne są najczęściej stosowane w procesach, gdzie zachodzi potrzeba oddzielenia dwóch lub trzech składników o wyraźnie różniących się temperaturach wrzenia. Z kolei destylatory kolumnowe charakteryzują się dużą powierzchnią kontaktu między parą a cieczą, co umożliwia bardziej efektywną separację wielu składników jednocześnie. Destylatory wirówkowe natomiast wykorzystują siłę odśrodkową do rozdzielania cieczy na podstawie gęstości, co czyni je idealnymi do separacji substancji o zbliżonych temperaturach wrzenia. Każdy z tych typów ma swoje unikalne zalety i ograniczenia, dlatego wybór odpowiedniego destylatora zależy od specyfiki procesu produkcyjnego oraz rodzaju przetwarzanych materiałów.
Jakie są kluczowe elementy konstrukcyjne destylatora przemysłowego
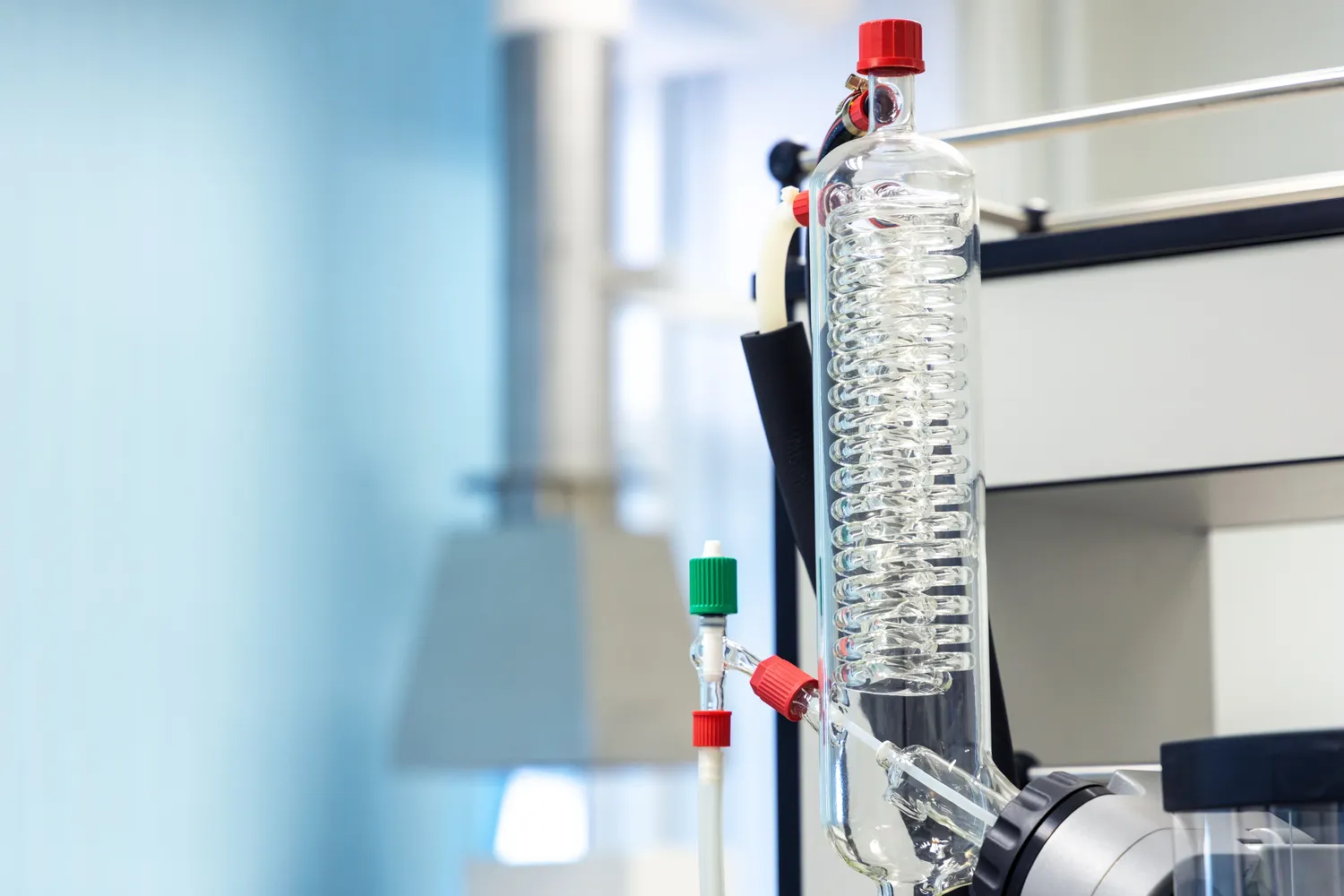
Konstrukcja destylatora przemysłowego opiera się na kilku kluczowych elementach, które mają istotny wpływ na jego działanie i efektywność. Do najważniejszych komponentów należy zbiornik do podgrzewania cieczy, który często wyposażony jest w grzałki elektryczne lub palniki gazowe. Kolejnym istotnym elementem jest kolumna destylacyjna, która może być wyposażona w różnego rodzaju packingi lub talerze, co zwiększa powierzchnię kontaktu pary z cieczą i poprawia efektywność separacji. Na końcu procesu znajduje się kondensator, który schładza parę i przekształca ją z powrotem w ciecz. Oprócz tych podstawowych elementów ważne są także systemy kontrolne oraz pomiarowe, które monitorują temperaturę i ciśnienie wewnątrz destylatora, co pozwala na optymalizację procesu. Współczesne destylatory mogą być także wyposażone w dodatkowe urządzenia filtracyjne czy pompy recyrkulacyjne, co zwiększa ich wszechstronność i umożliwia dostosowanie do różnych warunków pracy.
Jakie są korzyści z używania nowoczesnych destylatorów przemysłowych
Nowoczesne destylatory przemysłowe oferują szereg korzyści, które przyczyniają się do zwiększenia efektywności procesów produkcyjnych oraz redukcji kosztów operacyjnych. Przede wszystkim nowoczesne technologie umożliwiają osiąganie wyższej wydajności separacji dzięki zastosowaniu zaawansowanych materiałów i konstrukcji kolumny destylacyjnej. Dzięki temu możliwe jest uzyskanie czystszych produktów przy mniejszych stratach surowców. Kolejną zaletą jest automatyzacja procesów, która pozwala na zdalne monitorowanie i kontrolowanie parametrów pracy urządzenia. To nie tylko zwiększa bezpieczeństwo operacji, ale także pozwala na szybsze reagowanie na ewentualne problemy techniczne. Dodatkowo nowoczesne destylatory często charakteryzują się lepszą efektywnością energetyczną dzięki zastosowaniu innowacyjnych rozwiązań technologicznych takich jak odzysk ciepła czy inteligentne systemy zarządzania energią. W kontekście ochrony środowiska warto również wspomnieć o zmniejszeniu emisji szkodliwych substancji dzięki lepszym procesom oczyszczania oraz możliwości recyklingu odpadów powstających podczas produkcji.
Jakie są najczęstsze problemy związane z destylatorami przemysłowymi
Destylatory przemysłowe, mimo swojej zaawansowanej technologii, mogą napotykać różne problemy, które wpływają na ich wydajność oraz jakość uzyskiwanych produktów. Jednym z najczęstszych problemów jest zatykanie kolumny destylacyjnej, co może prowadzić do obniżenia efektywności separacji. Zatykanie to często spowodowane jest osadzaniem się zanieczyszczeń lub substancji o wysokiej lepkości, co utrudnia przepływ pary i cieczy. Innym istotnym problemem jest niestabilność temperatury, która może wynikać z niewłaściwego ustawienia grzałek lub nieefektywnego działania systemu chłodzenia. Wahania temperatury mogą prowadzić do niepożądanych reakcji chemicznych oraz obniżenia jakości końcowego produktu. Dodatkowo, niewłaściwe ciśnienie w systemie może powodować problemy z kondensacją pary, co również wpływa na wydajność procesu. Warto również zwrócić uwagę na kwestie związane z bezpieczeństwem, takie jak ryzyko wybuchu par czy pożaru w przypadku niewłaściwego użytkowania urządzenia.
Jakie są koszty związane z zakupem i eksploatacją destylatora przemysłowego
Koszty związane z zakupem i eksploatacją destylatora przemysłowego mogą być znaczne i zależą od wielu czynników, takich jak typ urządzenia, jego rozmiar oraz zastosowanie. Na początku warto zwrócić uwagę na cenę zakupu samego destylatora, która może sięgać od kilku tysięcy do nawet setek tysięcy złotych w przypadku dużych instalacji przemysłowych. Oprócz kosztów zakupu należy uwzględnić wydatki związane z instalacją oraz uruchomieniem urządzenia, które mogą obejmować prace budowlane, podłączenie mediów oraz szkolenie personelu. Kolejnym istotnym elementem są koszty eksploatacyjne, które obejmują zużycie energii elektrycznej lub paliwa do podgrzewania cieczy, a także koszty materiałów eksploatacyjnych takich jak środki czyszczące czy części zamienne. Warto również pamiętać o kosztach związanych z konserwacją i serwisowaniem urządzenia, które są niezbędne dla zapewnienia jego prawidłowego działania i wydajności.
Jakie innowacje technologiczne wpływają na rozwój destylatorów przemysłowych
Innowacje technologiczne mają ogromny wpływ na rozwój destylatorów przemysłowych i ich zdolność do efektywnej separacji substancji chemicznych. W ostatnich latach zauważalny jest trend w kierunku automatyzacji procesów destylacji, co pozwala na zdalne monitorowanie i kontrolowanie parametrów pracy urządzenia. Dzięki zastosowaniu nowoczesnych czujników oraz systemów informatycznych możliwe jest uzyskanie dokładnych danych o temperaturze, ciśnieniu czy przepływie cieczy w czasie rzeczywistym. To umożliwia szybsze reagowanie na ewentualne problemy oraz optymalizację procesów produkcyjnych. Kolejną innowacją są nowe materiały konstrukcyjne stosowane w budowie kolumn destylacyjnych, które charakteryzują się lepszą odpornością na korozję oraz wyższą efektywnością separacji. Przykładem mogą być powłoki nanostrukturalne lub materiały kompozytowe, które zwiększają powierzchnię kontaktu między parą a cieczą. Również rozwój technologii odzysku ciepła pozwala na zmniejszenie zużycia energii poprzez ponowne wykorzystanie ciepła generowanego podczas procesu destylacji.
Jakie są przyszłe kierunki rozwoju technologii destylacji przemysłowej
Przyszłość technologii destylacji przemysłowej zapowiada się obiecująco dzięki ciągłemu rozwojowi innowacyjnych rozwiązań oraz rosnącemu zainteresowaniu zrównoważonym rozwojem. Jednym z kluczowych kierunków jest dalsza automatyzacja procesów produkcyjnych, co pozwoli na jeszcze większą precyzję i efektywność operacyjną. Systemy sztucznej inteligencji mogą być wykorzystywane do analizy danych operacyjnych oraz prognozowania potencjalnych problemów zanim one wystąpią. Kolejnym ważnym aspektem będzie rozwój technologii odzysku energii oraz recyklingu odpadów powstających podczas procesu destylacji. Firmy będą coraz bardziej skupić się na minimalizacji wpływu swojej działalności na środowisko poprzez wdrażanie rozwiązań proekologicznych. Również rozwój nowych materiałów konstrukcyjnych może przyczynić się do poprawy efektywności energetycznej oraz trwałości urządzeń.
Jakie są regulacje prawne dotyczące używania destylatorów przemysłowych
Używanie destylatorów przemysłowych wiąże się z koniecznością przestrzegania szeregu regulacji prawnych dotyczących bezpieczeństwa pracy oraz ochrony środowiska. W wielu krajach istnieją szczegółowe przepisy dotyczące projektowania, budowy i eksploatacji urządzeń zajmujących się procesami chemicznymi, w tym destylacją. Przepisy te mają na celu zapewnienie bezpieczeństwa pracowników oraz minimalizację ryzyka wystąpienia awarii czy emisji szkodliwych substancji do atmosfery lub wód gruntowych. W Polsce regulacje te obejmują m.in. Ustawę o substancjach chemicznych oraz Ustawę o ochronie środowiska, które nakładają obowiązki na przedsiębiorców dotyczące monitorowania emisji oraz zarządzania odpadami powstającymi podczas produkcji. Ponadto wiele firm musi spełniać normy jakościowe ISO oraz inne standardy branżowe dotyczące bezpieczeństwa i jakości produktów końcowych.
Jakie są trendy rynkowe dotyczące destylatorów przemysłowych
Trendy rynkowe dotyczące destylatorów przemysłowych wskazują na rosnącą potrzebę innowacyjnych rozwiązań technologicznych oraz zwiększonego nacisku na efektywność energetyczną i ochronę środowiska. W ostatnich latach zauważalny jest wzrost zainteresowania automatyzacją procesów produkcyjnych, co pozwala firmom zwiększyć wydajność operacyjną i zmniejszyć koszty pracy. Również rosnąca świadomość ekologiczna społeczeństwa wpływa na decyzje zakupowe przedsiębiorstw – wiele firm poszukuje rozwiązań umożliwiających zmniejszenie śladu węglowego i ograniczenie zużycia surowców naturalnych. W odpowiedzi na te potrzeby producenci destylatorów inwestują w badania nad nowymi technologiami odzysku ciepła oraz recyklingu odpadów chemicznych powstających podczas procesów produkcyjnych. Dodatkowo obserwuje się wzrost znaczenia certyfikatów ekologicznych oraz norm jakościowych jako elementu konkurencyjności firm na rynku globalnym.