Budowa maszyn pneumatycznych opiera się na kilku kluczowych elementach, które współpracują ze sobą, aby zapewnić efektywne działanie systemu. Na początku warto zwrócić uwagę na sprężarki powietrza, które są sercem każdego układu pneumatycznego. Ich zadaniem jest sprężanie powietrza i dostarczanie go do reszty systemu. Kolejnym istotnym elementem są zbiorniki ciśnieniowe, które przechowują sprężone powietrze, umożliwiając jego późniejsze wykorzystanie w różnych procesach. W układzie pneumatycznym niezbędne są także zawory sterujące, które regulują przepływ powietrza oraz kierunek jego ruchu. Zawory te mogą być ręczne lub automatyczne, co pozwala na dostosowanie systemu do różnych potrzeb. Dodatkowo, w budowie maszyn pneumatycznych znajdują się siłowniki pneumatyczne, które przekształcają energię sprężonego powietrza w ruch mechaniczny. Siłowniki te mogą mieć różne kształty i rozmiary, co sprawia, że są wszechstronnie stosowane w różnych aplikacjach przemysłowych.
Jakie są zalety i wady maszyn pneumatycznych
Maszyny pneumatyczne mają wiele zalet, które przyciągają uwagę inżynierów i przedsiębiorców. Przede wszystkim ich konstrukcja jest stosunkowo prosta, co ułatwia ich montaż oraz konserwację. Dzięki temu można szybko reagować na ewentualne awarie i minimalizować przestoje w produkcji. Kolejną zaletą jest ich wydajność energetyczna – sprężone powietrze jest łatwe do pozyskania i może być wykorzystywane w wielu procesach bez potrzeby stosowania skomplikowanych układów zasilających. Maszyny pneumatyczne są także bezpieczniejsze w użytkowaniu niż ich elektryczne odpowiedniki, ponieważ nie ma ryzyka porażenia prądem. Jednakże istnieją również pewne wady związane z ich użytkowaniem. Jedną z nich jest ograniczona moc – maszyny pneumatyczne nie zawsze są w stanie wygenerować tak dużą siłę jak maszyny hydrauliczne czy elektryczne. Ponadto, sprężone powietrze może być kosztowne w produkcji i wymaga odpowiednich systemów filtracji oraz osuszania, aby uniknąć problemów związanych z wilgocią i zanieczyszczeniami.
Jakie zastosowania mają maszyny pneumatyczne w przemyśle
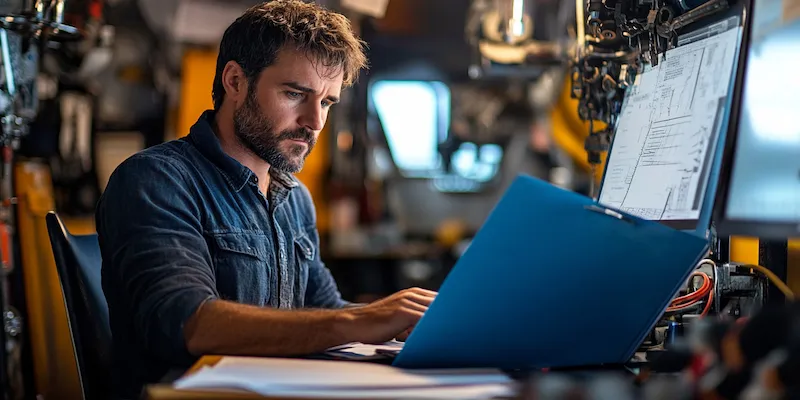
Maszyny pneumatyczne znajdują szerokie zastosowanie w różnych branżach przemysłowych dzięki swojej wszechstronności oraz efektywności działania. W przemyśle motoryzacyjnym często wykorzystuje się je do montażu i demontażu elementów pojazdów, gdzie precyzyjne sterowanie ruchem jest kluczowe dla jakości produkcji. W zakładach produkcyjnych maszyny pneumatyczne służą do transportu materiałów oraz komponentów na liniach montażowych, co znacznie przyspiesza procesy logistyczne. W branży spożywczej maszyny te są używane do pakowania produktów oraz napełniania pojemników, co zapewnia wysoką wydajność i higienę procesu. Również w sektorze budowlanym maszyny pneumatyczne odgrywają istotną rolę – wykorzystywane są do narzędzi takich jak młoty udarowe czy wiertnice, które wymagają dużej mocy przy jednoczesnej precyzji działania. W ostatnich latach zauważalny jest również wzrost zastosowania technologii pneumatycznych w automatyce przemysłowej, gdzie integracja z systemami sterowania pozwala na jeszcze większą efektywność produkcji oraz oszczędności energetyczne.
Jakie innowacje wpływają na rozwój maszyn pneumatycznych
Rozwój technologii wpływa na ewolucję maszyn pneumatycznych, a innowacje pojawiające się na rynku znacząco poprawiają ich funkcjonalność oraz efektywność. Jednym z najważniejszych trendów jest miniaturyzacja komponentów, co pozwala na tworzenie bardziej kompaktowych systemów o dużej mocy roboczej. Dzięki temu możliwe jest zastosowanie maszyn pneumatycznych w miejscach o ograniczonej przestrzeni bez utraty wydajności. Kolejnym istotnym aspektem jest rozwój inteligentnych systemów sterowania, które umożliwiają automatyzację procesów oraz monitorowanie pracy maszyn w czasie rzeczywistym. Wprowadzenie czujników i technologii IoT (Internet of Things) pozwala na zbieranie danych dotyczących pracy urządzeń oraz ich optymalizację poprzez analizę tych informacji. Również materiały wykorzystywane do produkcji elementów maszyn ulegają zmianom – nowoczesne tworzywa sztuczne oraz kompozyty zwiększają trwałość i odporność na uszkodzenia mechaniczne oraz korozję. Innowacje te przyczyniają się do zwiększenia efektywności energetycznej maszyn pneumatycznych oraz zmniejszenia kosztów eksploatacji, co czyni je bardziej konkurencyjnymi na rynku przemysłowym.
Jakie są najczęstsze problemy w budowie maszyn pneumatycznych
Budowa maszyn pneumatycznych, mimo wielu zalet, wiąże się z pewnymi wyzwaniami i problemami, które mogą wpływać na ich efektywność oraz niezawodność. Jednym z najczęstszych problemów jest nieszczelność układu, która może prowadzić do utraty ciśnienia i obniżenia wydajności maszyny. Nieszczelności mogą występować w różnych miejscach, takich jak połączenia przewodów, zawory czy siłowniki. Dlatego regularna konserwacja i kontrola stanu technicznego elementów układu są kluczowe dla zapewnienia prawidłowego działania. Innym istotnym problemem jest zanieczyszczenie sprężonego powietrza, które może prowadzić do uszkodzenia komponentów oraz obniżenia jakości produkcji. Zanieczyszczenia mogą pochodzić z różnych źródeł, takich jak wilgoć, pył czy oleje, dlatego stosowanie odpowiednich filtrów oraz osuszaczy jest niezbędne. Ponadto, niewłaściwe dobranie parametrów pracy maszyny do specyfiki zastosowania może prowadzić do jej przegrzewania lub nadmiernego zużycia energii. Warto również zwrócić uwagę na konieczność stosowania odpowiednich narzędzi i akcesoriów, które są dostosowane do konkretnego modelu maszyny pneumatycznej.
Jakie są różnice między maszynami pneumatycznymi a hydraulicznymi
Maszyny pneumatyczne i hydrauliczne to dwa różne typy systemów wykorzystywanych w przemyśle, które mają swoje unikalne cechy oraz zastosowania. Główna różnica między nimi polega na medium roboczym – maszyny pneumatyczne wykorzystują sprężone powietrze, podczas gdy maszyny hydrauliczne działają na zasadzie cieczy hydraulicznych. Dzięki temu maszyny hydrauliczne mogą generować znacznie większe siły niż ich pneumatyczne odpowiedniki, co czyni je idealnymi do zastosowań wymagających dużej mocy, takich jak prasy czy dźwigi. Z drugiej strony, maszyny pneumatyczne charakteryzują się większą szybkością działania oraz prostotą konstrukcji, co sprawia, że są często stosowane w aplikacjach wymagających precyzyjnego sterowania ruchem. Kolejną różnicą jest bezpieczeństwo użytkowania – sprężone powietrze jest mniej niebezpieczne niż ciecz hydrauliczna, która może powodować poważne awarie w przypadku wycieku. Koszty eksploatacji również różnią się – sprężone powietrze jest łatwiejsze do pozyskania i tańsze w utrzymaniu niż oleje hydrauliczne.
Jakie są przyszłe kierunki rozwoju technologii maszyn pneumatycznych
Przyszłość technologii maszyn pneumatycznych zapowiada się obiecująco dzięki ciągłemu rozwojowi innowacji oraz rosnącemu zapotrzebowaniu na efektywne rozwiązania przemysłowe. Jednym z kluczowych kierunków rozwoju jest integracja maszyn pneumatycznych z nowoczesnymi systemami automatyki i robotyki. Dzięki temu możliwe będzie stworzenie bardziej zaawansowanych linii produkcyjnych, które będą mogły działać autonomicznie i dostosowywać się do zmieniających się warunków pracy. Wprowadzenie sztucznej inteligencji do procesów sterowania pozwoli na optymalizację pracy maszyn oraz lepsze zarządzanie zasobami energetycznymi. Również rozwój materiałów kompozytowych i lekkich stopów metali przyczyni się do zwiększenia efektywności energetycznej maszyn pneumatycznych oraz poprawy ich trwałości. W kontekście ochrony środowiska coraz większą wagę przykłada się także do redukcji hałasu generowanego przez maszyny pneumatyczne oraz minimalizacji ich wpływu na otoczenie. Wprowadzenie technologii recyklingu sprężonego powietrza oraz systemów odzysku energii stanie się standardem w nowoczesnych zakładach przemysłowych.
Jakie są koszty związane z budową maszyn pneumatycznych
Koszty związane z budową maszyn pneumatycznych mogą być zróżnicowane w zależności od wielu czynników, takich jak skomplikowanie projektu, rodzaj użytych komponentów oraz skala produkcji. Na początku należy uwzględnić koszty zakupu podstawowych elementów systemu, takich jak sprężarki powietrza, zbiorniki ciśnieniowe czy zawory sterujące. Ceny tych komponentów mogą się znacznie różnić w zależności od producenta oraz jakości materiałów użytych do ich produkcji. Kolejnym istotnym aspektem są koszty montażu i uruchomienia maszyny – zatrudnienie specjalistów do instalacji oraz kalibracji urządzeń może znacząco wpłynąć na całkowity koszt inwestycji. Nie można także zapominać o kosztach eksploatacyjnych związanych z utrzymaniem sprawności systemu – regularne przeglądy techniczne, wymiana filtrów czy konserwacja sprężarek to niezbędne wydatki, które należy uwzględnić w budżecie. Dodatkowo warto rozważyć inwestycję w nowoczesne technologie monitorowania pracy maszyn, które mogą pomóc w optymalizacji kosztów operacyjnych poprzez identyfikację potencjalnych problemów zanim staną się one poważnymi awariami.
Jakie są najnowsze trendy w projektowaniu maszyn pneumatycznych
Najnowsze trendy w projektowaniu maszyn pneumatycznych koncentrują się na zwiększeniu efektywności energetycznej oraz automatyzacji procesów przemysłowych. Coraz więcej producentów stawia na rozwój inteligentnych systemów zarządzania pracą maszyn, które umożliwiają monitorowanie ich stanu w czasie rzeczywistym oraz dostosowywanie parametrów pracy do aktualnych potrzeb produkcyjnych. Integracja technologii IoT pozwala na zbieranie danych dotyczących wydajności urządzeń oraz ich optymalizację poprzez analizę tych informacji. Kolejnym istotnym trendem jest miniaturyzacja komponentów – dzięki nowoczesnym materiałom i technologiom produkcji możliwe jest tworzenie mniejszych i bardziej kompaktowych jednostek roboczych bez utraty wydajności czy mocy roboczej. Również ekologia staje się coraz ważniejszym aspektem projektowania maszyn pneumatycznych – producenci starają się ograniczać zużycie energii oraz emisję hałasu poprzez wdrażanie innowacyjnych rozwiązań technologicznych.